Inspection or surface preparation
A thorough surface preparation of a substrate is essential for the performance of a coating system. It can best be compared with the foundation of a building. If the foundation is not solid, the building’s integrity will be compromised.
The durability of a paint system is highly influenced by the quality of surface preparation. The inspection of the surface preparation is by far the most important control step in the total coating process.
In the coating industry a wide range of preparation methods are available and are defined under ISO, NACE, SSPC and other international standards. DCC has knowledge of all common standards and specifications and a vast experience with methods for the assessment of surface cleanliness, surface roughness as well as other surface preparation related tests. In addition to corrosion protection through application of traditional coating systems, there are other methods such as hot-dip galvanizing and spray metallization. DCC also is experienced in performing inspections related to these techniques as well. At the start of a project it is important for inspectors, representatives of clients, contractors and paint suppliers to agree on test methods for a project to avoid differences of interpretation at a later stage. A good coating specification provides clear guidance with regard to, among other things, the test methods to be utilized as well as all criteria for acceptation or and rejection of any work.
Click here for an overview of the most common test methods for surface preparation.
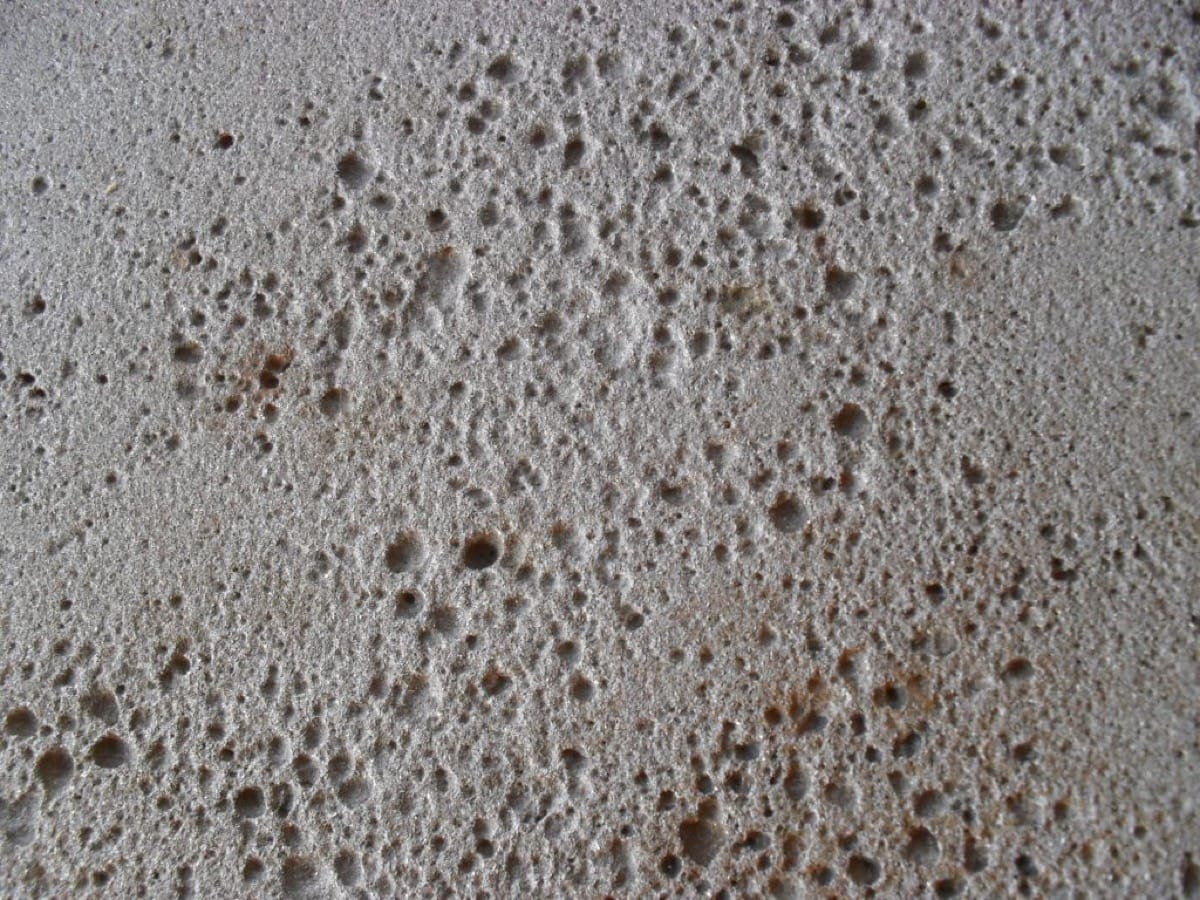
Cleanliness
The durability of a coating system for both aesthetic and preservation purposes largely depends on the level of cleanliness of the substrate. Cleanliness is acquired by using one of many different methods of surface preparation to remove rust and old coating. Insufficient cleanliness will directly influence the protective properties of the coating film and specifically its adhesion to the substrate. A required level of cleanliness can be obtained by using different techniques. Chemical treatment of a substrate, Ultra High Pressure water Jetting, hand or power tool cleaning or wet and dry abrasive blasting can be used. In a proper coating specification the required grade of preparation is specified by referring to one of many international standards such as ISO 8501-1, ISO 8501-2, NACE 1/SSPC-SP5, NACE 2/SSPC-SP10, NACE 3/SSPC-SP6, NACE 4/SSPC-SP7 or NACE WJ-1/SSPC SP WJ-1. DCC has the knowledge and experience to correctly assess the level of cleanliness of substrates based on the requirements of a specification or guidelines provided by the coating manufacturer.
Surface profile
The durability of a coating system for both aesthetic and preservation purposes is partially depending on the level of adhesion of the coating system. Adhesion depends on the level of roughness/surface profile of the prepared surface. Insufficient surface profile will directly, negatively influence the adhesion of the coating system. Surface profile can be obtained by the use of a number of surface preparation techniques. Some techniques will however produce little to no surface roughness which will influence the selection of a coating system. Surface profile, also referred to as anchor profile, is considered to be one of the most important aspects of surface preparation. Certain specific coating products will largely depend on surface profile for their adhesion to the substrate. The different methods and units used to express the results are a common cause for confusion. DCC has the knowledge, experience and the advanced equipment to measure surface profile and correctly interpret the results of the readings prior to coating application based on requirements mentioned in the coating specification or guidelines provided by the coating manufacturer. Click here to see the overview of the most common methods.
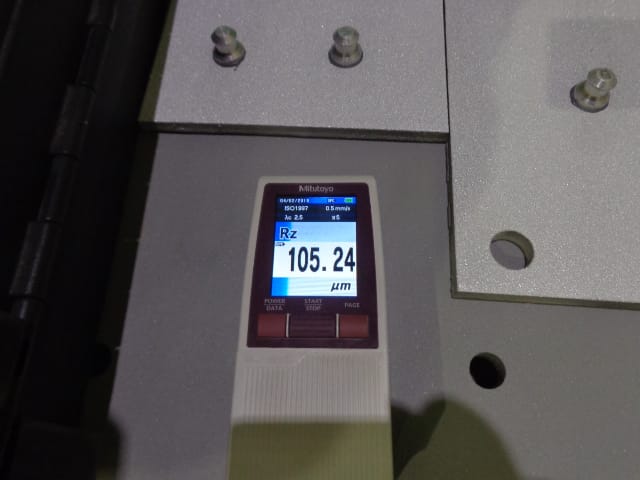
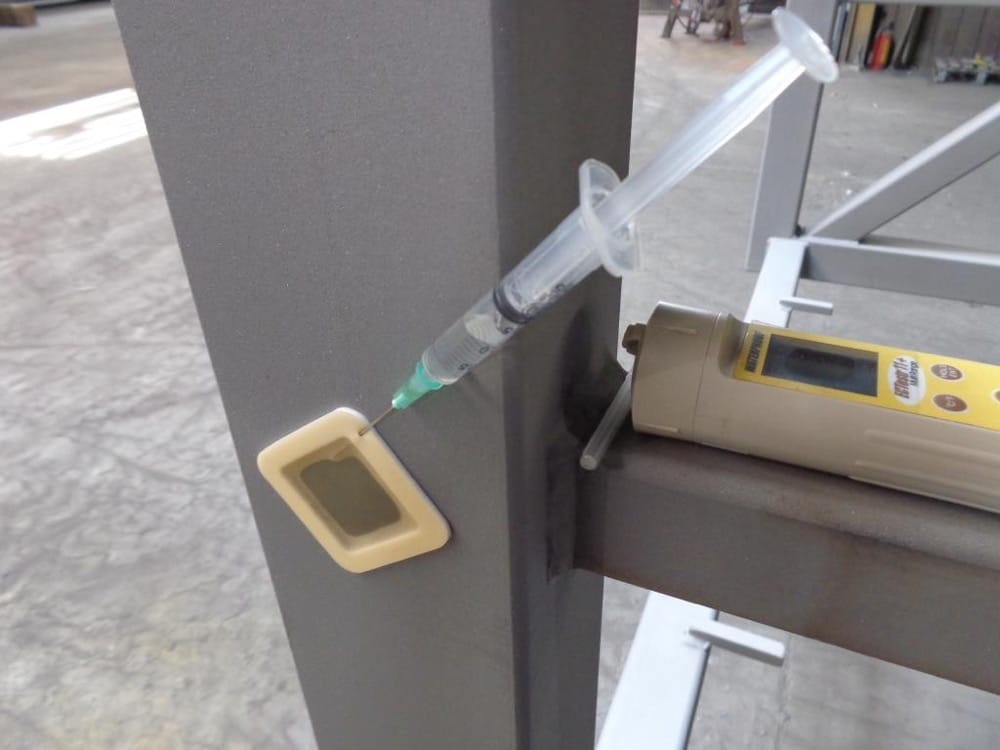
Non visible contamination
Also a possible contamination with non-visible contaminants will influence the durability of a coating system. Non visible contamination refers to types of contamination that cannot be spotted with the naked eye but who’s presence can be tested and measured using specific test methods. Non visible contamination is primarily water soluble contamination found on the surface to be coated. It is common to (only) focus on chloride contamination, however there are many other potential sources for soluble contamination. Industrial process may emit sulphates and or nitrates as part of exhaust fumes or agricultural use. All of these may result in the deposition of water soluble contamination of the substrate. The presence of water soluble contamination on a metal surface may result in blistering of the coating film (osmosis) specifically when the coating system is used in an immersion service. Soluble salts have a natural tendency to attract water resulting in blistering of the coating film. In the case of stainless steel the presence of water soluble chloride contamination will provided on of the key elements for the development of chloride stress corrosion. Non visible contamination can be measured using a number of different methods. There is a lot of confusion on the subject of soluble contamination methods. DCC has the knowledge, experience and the advanced equipment to measure the presence of non-visible contamination and to correctly interpret the results of the readings based on requirements mentioned in the coating specification or guidelines provided by the coating manufacturer.
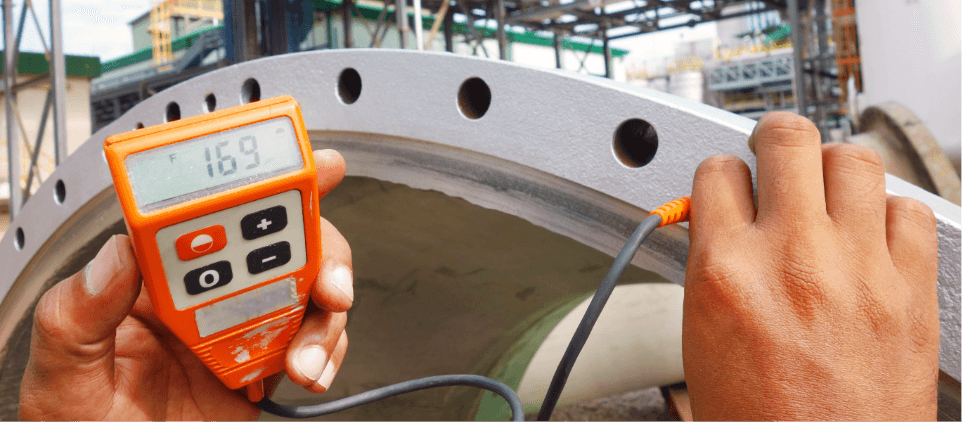