Detection of mill scale
Failure to completely remove mill scale is a common cause of premature failure of a coating system. Mill scale behaves cathodic (more noble) relative to the steel substrate.
Mill scale is the typical blue/black layer of oxide that is formed during the production of hot rolled steel. The thickness of the mill scale varies from 50 to 500 microns depending on the rolling conditions and the quality of the steel. When mill scale is not fully removed and is subsequently painted over this will ultimately, depending on time and exposure conditions, result in corrosion under the coating system. Reason for this is the fact that mill scale behaves cathodic to steel. At the point where moisture is able to penetrate the coating system and reach the mill scale a corrosion cell is formed were the steel behaves anodic (sacrificial) to the mill scale.
It is not uncommon for contractors to blast new steel using shot blast equipment. Pure shot (round abrasives) as an abrasive is less effective in the removal of mill scale.(Steel) shot has no cutting effect and removal of corrosion and mill scale therefore depends on the “hammering” effect of the abrasive (kinetic energy). The practical problem is that all standards that are used for the evaluation of the levels of cleanliness of blasted steel are visual standards. It is possible that mill scale, although present, is not visually recognizable as such. Experiences with various large projects have shown that residual mill scale is a common cause for premature failure of coating systems.
DCC is able to test the presence of mill scale using different techniques such as visual examination (cross section preparation of coating films), assessment of Ferro magnetic properties and lab analysis such as SEM/EDS. In addition to this DCC can carry out so called copper sulphate tests according to ASTM A-380 during the blasting process, providing contractors with independent expertise to ensure mill scale is adequately removed in their (automated) shot blasting process.
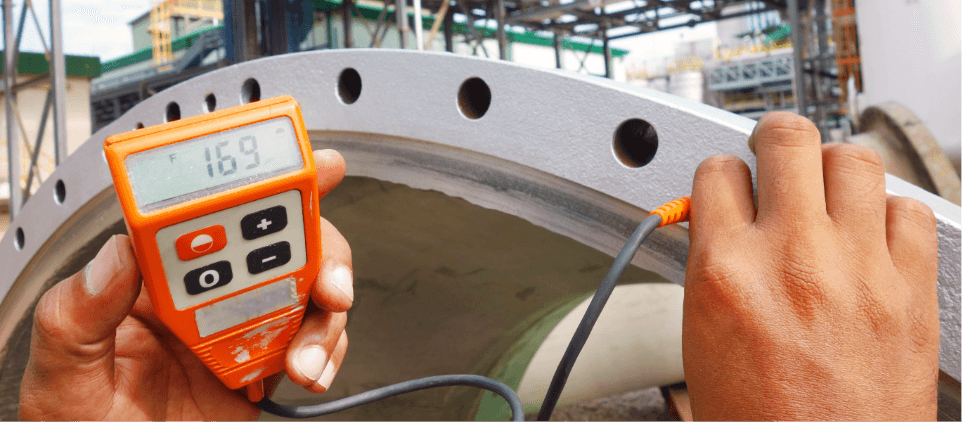